A look inside
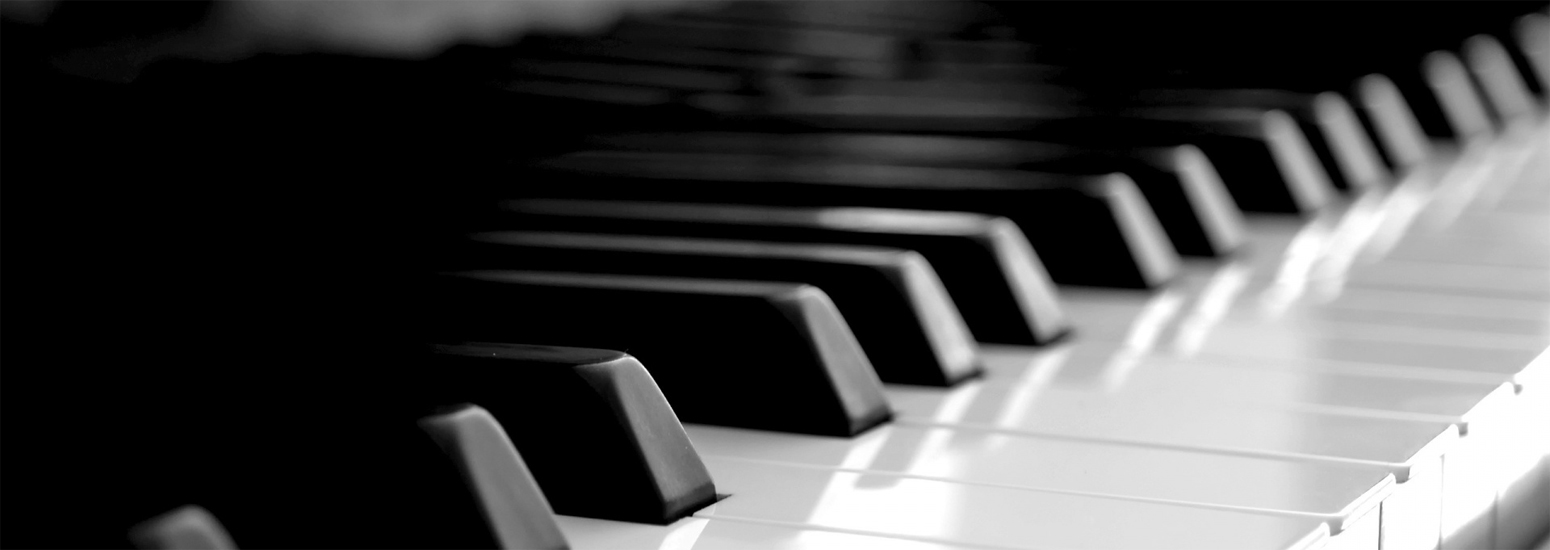
In analogy to a gourmet meal, only the perfect method of preparation allows outstanding results, the simple use of excellent ingredients will never be a a guarantor for authentic culinary delights for gourmets.
Building a loudspeaker is similar. But with one important difference. A gourmet meal will be judged on the unique merit of its taste making the notion of "true" and "false" meaningless, completely contrary to what audio engineering is all about.
The foundation and basis for the excellent performance of our products is the cabinet. All cabinets of ARTOS are optimised to keep resonance effects as low as possible, while using the energy radiated into the cabinet instead of absorbing it.
The shape of our cabinets and their internal construction allow optimal air flow efficiency while keeping resonances at a minimum. Thus, we are able to avoid the use of any damping materials inside the cabinets.
We have experimented with many different materials and measured their mechanical. Birch, Beech and Maple are the woods used to manufacture our cabinets. Eleven layers of different kind of wood are pressed into shape for the side walls, while the front baffle uses a massive and solid piece of beechwood.
The extreme stiffness and resonance poperties of our cabinets avoid the typical "wooden" sound, which is known for less elaborate constructions.
Building a loudspeaker is not a mystic thing, really: mount a woofer and a tweeter in a solid box, shelter the tweeter from low frequency vibration and filter high frequencies out of the woofer's signal - finished! Something audible will emerge from that and someone will either like or not.
Placing the highest demands on our developments turns every smallest detail into a time- and cost intensive project.
Even the manufacturing process of the cabinets for one pair of our smallest loudspeaker SUNRISE requires 100 working hours. First, the side panels are pressed into shape. After this, the CNC-machined front baffle and the rear Air-Flow-panel are mounted to the side panels using numerous internal braces. Next, the cabinet is sealed and lacquered inside using a special instrument varnich.
The selection of the exclusive wood veneers and their processing requires a high degree of perfected technical skills, style competence, artistic talent, expert knowledge and - last but not least - a great love of detail. Indian Appletree, Bubinga, Service Tree, Eukalytus or french Nut - every veneer is selected for a perfect fit on the cabinet it is used for.
Timeless in appearance, noble and with perfect finish, these are properties of the piano lacquer we use. We've chosen high-gloss lacquer as standard finish for all our loudspeakers, it is the visual expression of the superior technical standard of our products.
The coating consist of many layers applied in consecutive steps and is subject to a number of polishing processes at the end of which stands a very meticulous manual high gloss polish. High-gloss piano lacquer belongs without any doubt in the champions' discipline of surface treatment and, we daresay, at these unique levels of quality and finish it is the sure winner.
At the very heart of every loudspeaker, the drivers are of crucial importance to ARTOS. Our specialist supplier Thiel & Partner manufacture Accuton drivers after our individual requirements, unique Original Equipment Manufacturer products for exclusive use by ARTOS.
The decisive factor in our selection of a driver is its coherent behaviour with the cabinet and the crossover filter in the finished loudspeaker. Because of this, unrelated appraisals and general conclusions on the quality of chassis have no validity.
For all our modells, we are using ceramic drivers made by Thile & Partner.
These drivers behaves like perfect pistons for moving air, and on top of that they are light as a feather. However, these extremely rigid diaphragms can also produce considerable resonances that objectionably interfere with the original signal, modify it and are a source of coloration. Without perfect filter, one will always hear the driver's diaphragm.
Thiel & Partner's exorbitantly expensive Black-Diamond-Tweeter that we assemble in our Diamond-Series loudspeakers raises the bar even higher. Unfortunately, this is the most expensive tweeter in the world costing more than many other complete speaker systems.
Needless to say, that we pay particular attention to our crossovers, so that no trace of colouration will persist. An ARTOS will therefore never present the sound of ceramic or diamond, but solely music. Consequently, it is an invalid assumption that our speakers will sound like other constructions that happen to feature the same materials.
The crossover can be regarded as the brain and the heart of a loudspeaker. It “rules” the way of frequencies, influeces the linearity and impedance behaviour of the loudspeaker and is responsible for the efficiency of the entire system.
At ARTOS, we are using cast pure silver foil capacitors, coils of the same caliber, extremely low resistance inductors and silver-carbon resistors - only the finest components with proven long time stability.
Unfortunately, these components belong to the most expensive in the world as well. For example: the crossover for our reference modell HURRICANE costs more than a pair of new SUNRISE's in precious wood finish.
Whether any part must be that expensive is a meaningless question and, for one thing, not one that should arise from budgetary restraints. Only the final result is what counts to us and considerations of cost do not enter into the equation.
Our guiding principle is to present our customers with the highest possible degree of reality in music reproduction. Anything less is already available but does not meet our demands.